Cars
Our Latest Challenger: FE11
For the first time since 2019, FE11 passed all technical inspections and competed in all four dynamic events at competition, marking a major milestone for FRUCD. Coming off a challenging previous year, the team’s determination and hard work propelled us to a 22nd place finish out of 89 teams, with standout top-10 performances in Autocross and Cost. Notably, we ranked 2nd among California teams.
While a BSPD fault ended our endurance run early, this car demonstrated our ability to bounce back stronger and push the limits of our engineering capabilities.
FE11’s improvements were focused on manufacturability and reliability with an aim to build a strong foundation for future years. Some notable achievements are reducing the chassis by 21 tubes and 8 pounds in weight, decreasing wheel package manufacturing time by 16x, and being able to drive FE11 at the UC Davis Picnic Day parade, occurring 3 months before competition.
Weight: 220.0 kg (without driver)
Weight Balance: 51.1% Front | 49.4% Left
Electric Motor: EMRAX d.o.o, EMRAX 228 HV LC
Output: 50kW peak, 20kW continuous
Max Torque: 230 Nm
Accumulator: Molicel/21700 Cylindrical
Maximum design speed: 81 mph
Chassis: Space frame 1020 Steel Round Tubing
Competition Results: 22nd Overall, 6th Cost, 7th Autocross, 13th Skidpad, 17th Acceleration, 34th Design, 38th Business
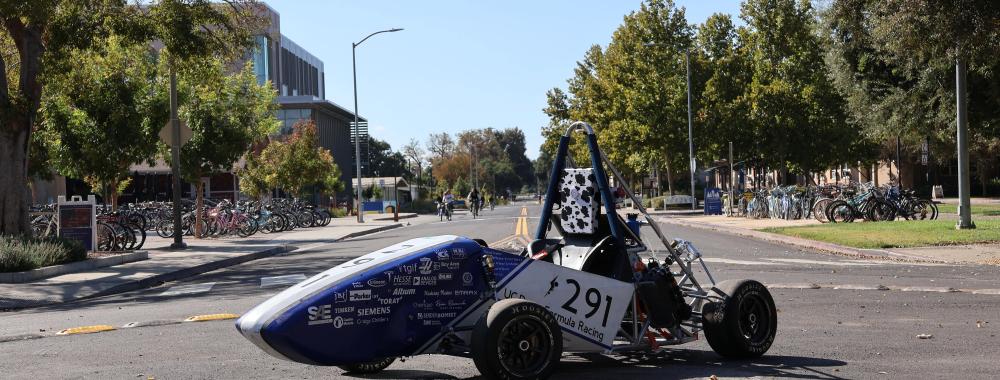
FE10
In the 2022-23 academic year, FRUCD introduced FE10 to the world, participating in the FSAE competition. Recovering from the COVID-19 pandemic, our leads are gaining valuable practice participating.
FE10 introduced our first ever aerodynamic package, with a brand new front wing made of carbon fiber. Furthermore, improvements were made on the chassis and manufacturing was smoothened to help boost production progress.
Weight: 233.99 kg (without driver)
Weight Balance: 49.6% Front | 49% Left
Electric Motor: EMRAX d.o.o, EMRAX 228 HV LC
Output: 50kW peak, 20kW continuous
Max Torque: 230 Nm
Accumulator: Molicel/21700 Cylindrical
Maximum design speed: 81 mph
Chassis: Space frame 4130 Steel Circular Tubing
Notable Features: Carbon fiber seat, first aerodynamic package
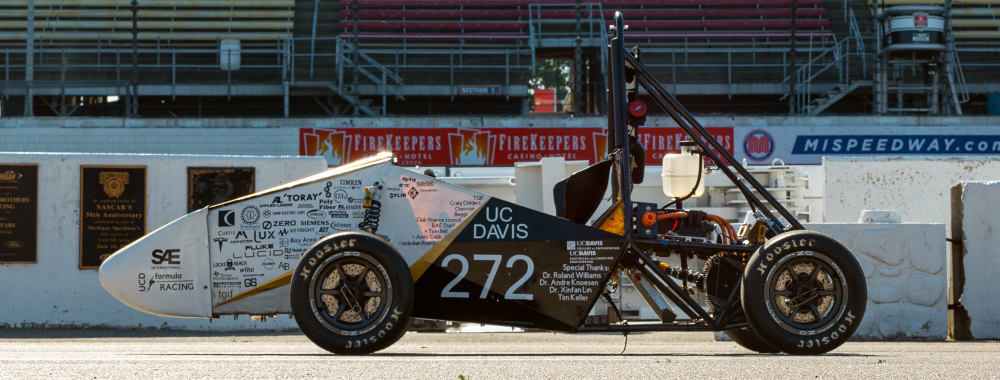
FE9
After recovering from the COVID-19 pandemic, FRUCD participated in the FSAE competition for the 2021-22 academic year with their FE9 Vehicle, which was our first physical car built for the competition post-pandemic.
The FE9 underwent various updates, including the creation of exterior body panels by the Composites subteam that focused on both rigidity and aesthetics. We used carbon fiber to minimize weight of the driver’s seat. Additionally, the pedal box floor became the first carbon fiber structural part, demonstrating the potential to produce more successful carbon pieces.
The Firmware subteam added in-house Battery Management System firmware to the electrical subgroup, centralized vehicle state machine, previously on the dashboard and a separate node, in the Vehicle Control Unit.
The Accumulator subteam successfully switched to 18650 cylindrical cells for higher energy density and gravimetric density so the cells were actively cooled with external fans forcing air through heatsinks. The Drivetrain subteam reduced weight of the car while maintaining a reliable and robust system and implemented a new water cooling plate design for the motor controller.
While the Vehicle Dynamic subteam worked on the performance envelope, vehicle model, optimizing and justifying controls, suspension, and wheel package, Suspension subteam allowed for better shock packaging for half-shaft clearance while retaining easy rear camber adjustability. Moreover, Controls subteam optimized pedal box for weight reduction and manufacturability, validated steering system choice with research. The Wheel Package subteam reduced the weight while keeping structural strength and rigidity, optimized tunability of camber and suspension clearance at outboard pickup points.
Year Produced: 2021-2022
Weight: 198.6 kg (without driver)
Weight Balance: 49.6% Front | 49.9% Left
Electric Motor: Zero Z-Force 75-7R
Output: 50kW peak, 20kW continuous
Max Torque: 158Nm
Accumulator: custom battery packs with 18650 cells, (5s24p)5p configuration, integrated forced air cooling
Battery Capacity: 6.74kWh
Chassis: Space frame 4130 chromoly steel
Notable Features: Carbon fiber seat, first carbon fiber structural part (pedalbox floor), water cooled motor controller
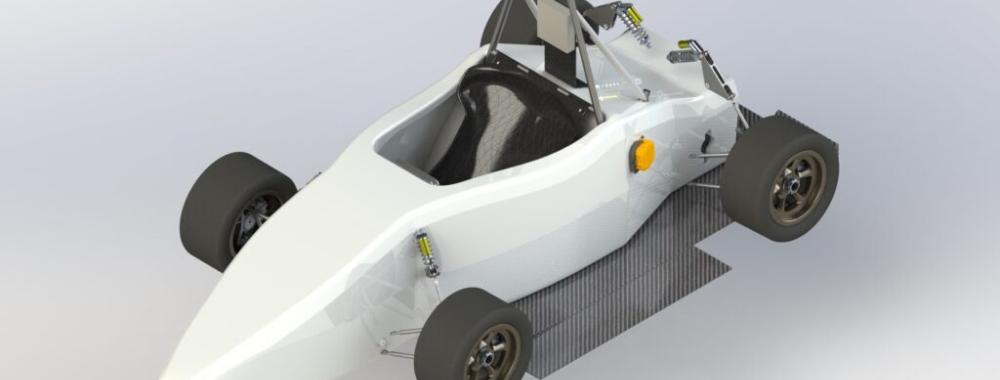
FE8
With the rise of COVID-19 cases, UC Davis has extended remote learning for the 2020-2021 school year. Although it put the team’s testing and manufacturing schedule on hold, the team continued to work remotely on the development of the car with a focus primarily on methods for design in preparation for the next season.
In October, it was announced by UC Davis that work on a new expansion of the on-campus machine shop and student team space would begin. In order to secure a space for testing and assembly, FRUCD maintained close communication with the College of Engineering. This effort was successful, and the college pledged to secure a workspace for the teams after the University’s return to full operation once the quarantine for COVID had been lifted. The new workspace would be smaller than the previous space and the team would not have access to certain capabilities such as a waterjet or a full welding table setup, and would only have access to two CNC mills, two CNC Lathes, a CNC Router, and a smaller MIG Welder.
One of the major developments of FE8 is the Composite Monocoque. The Structures subgroup made the switch from Steel Tube Frame to Composite Monocoque, which provided a higher stiffness and more flexibility with the Suspension mounting locations. The Monocoque geometry also benefited the suspension team to improve stability.
As for the Electrical subgroup, the High Voltage subteam emphasized improving temperature management of the accumulator and increasing Battery Management System response time while the Low Voltage subteam focused on strengthening system reliability and developing a data acquisition system. This provided track data which helped with informing other subteam’s design decisions.
The Powertrain subgroup continued to improve the cooling of critical components, including the motor controller and motor along with reducing weight and component costs. In order to enhance the energy performance, the Accumulator subteam switched from pouch cells to cylindrical cells for a higher energy density and adopted heatsinks to prevent thermal attenuation.
In addition, the Unsprung subgroup focused on developing tire models and lap time simulators to further refine vehicle targets. The Wheel Package team made a significant reduction in the subsystem weight and compliances, while the Controls subteam enhanced the sterling wheel and pedal box for smooth integration into the monocoque. The Aerodynamics subteam emphasized cooling models validation and drag reduction.
Overall, the collaborative effort from team members working from their desks brought FE8 to 117V and 441lbs.
Year Produced: 2020-2021
Weight: 441 lb
Weight Balance: 48.0% Front| 50.5% Left
Electric Motor: EMRAX 228 HV LC
Output: 130 kW @ 5500 RPM
Max Torque: 230 N-m for 3 sec
Max Speed: 74.6 mph (120 kph)
Accumulator: Melasta Li-Ion
Battery Capacity: 0.038 kWh
Suspension:
Front: Unequal Length Double Wishbone w/ Direct Acting Shock
Rear: Unequal Length Double Wishbone w/ Pushrod
Chassis: Monocoque
Notable Features: CFRP seat, headrest, nosecone, and nose-flap
Drexler Limited Slip Differential
4.5m turning radius for increased dynamic performance
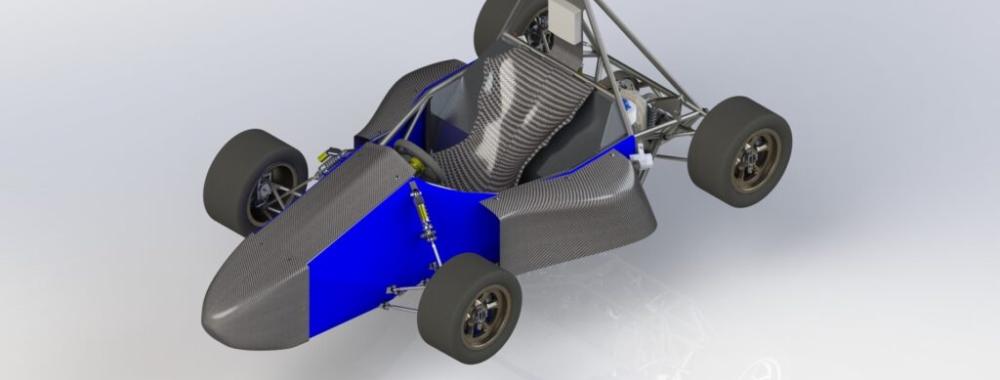
FE7
With FE6’s thermal conditions, FE7 placed emphasis on optimizing the cooling system performance. Other team-wide goals included refining reliability, documentation, and the process of knowledge transfer.
The Powertrain subsystem integrated a water-cooled system that provided sufficient rejection rates of predicted wattage. The Accumulator team was built to be water-cooled and compliant with the FSAE rules. In addition, the Aerodynamics team provided support to the cooling system by performing cooling validation and incorporated sidepods for the first time to provide adequate airflow through radiators.
Meanwhile, other subsystems worked towards enhancing past year’s designs. The Wheel Package team made improvements on outboard braking components with the use of a floating rotor and connections with suspension. The Chassis team expanded the knowledge base on stiffness and reduced its length while complying with the minimal weight. Moreover, Suspension was also optimized to allow for parts to be serviced while giving clearance to other subsystems.
However, FRUCD’s development cycle for FE7 was cut short due to a University mandated quarantine associated with COVID-19. This meant that all student teams were prevented from accessing the workshop and working on the vehicle.
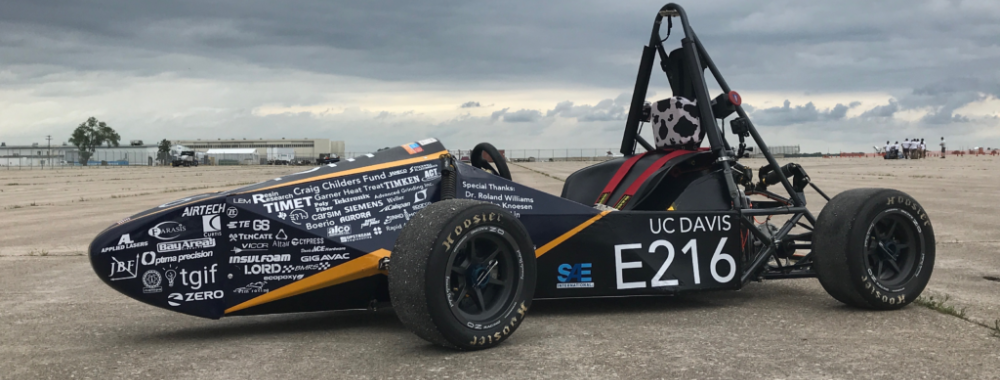
FE6
After several iterative years, FE6’s design included significant changes that better aligned our vehicle’s performance with the top EV teams. As a whole, the team focused on re-establishing and solidifying fundamental understandings of subsystems to promote documentation for future years, and ensured product control through attention to subsystem interfaces and organizational measures.
Following FE5’s electrical system failure to pass its technical inspection due to water entry, additional emphasis was placed on designing effective seals and water pathways. For the first time, active cooling was implemented using fans to force air through the battery. Internal baffles and adjustable fan speeds based on thermal conditions were used to evenly and effectively regular internal temperatures. FE6 also featured the team’s first 10” wheel package, designed to improve steering angle and reduce unsprung weight, and created an opportunity to use a Drexler clutch-pack LSD. FE6’s body panels remained aircraft fabric, while the nosecone, top cover, and seat were manufactured from carbon fiber for the first time.
Testing prior to competition was used to tune FE6 for optimal performance and identify any durability concerns, especially regarding systems related to the all-new wheel package and differential. Thanks to the team’s attention to detail, drive, and determination; FE6 placed 4th overall, 3rd in the United States, placed 2nd in Endurance and 2nd in Cost at the FSAE Electric competition.
Year Produced: 2018-2019
Weight: 449 lb
Weight Balance: 49.0% Front| 50.2% Left
Electric Motor: ZERO Z-Force 75-7R
Output: 50 kW @ 3850 RPM
Max Torque: 140 N-m for 120 sec
Max Speed: 80 mph
Accumulator: NCM-Cathode Li-Ion
Battery Capacity: 6.1 kWh
Suspension: Double Unequal A-Arm with Pushrod Actuated Shock Absorber
Chassis: 4130 Steel Space Frame
Notable Features: Carbon Fiber seat, headrest, nosecone, and nose-flap
Drexler Limited Slip Differential
4.5m turning radius for increased dynamic performance
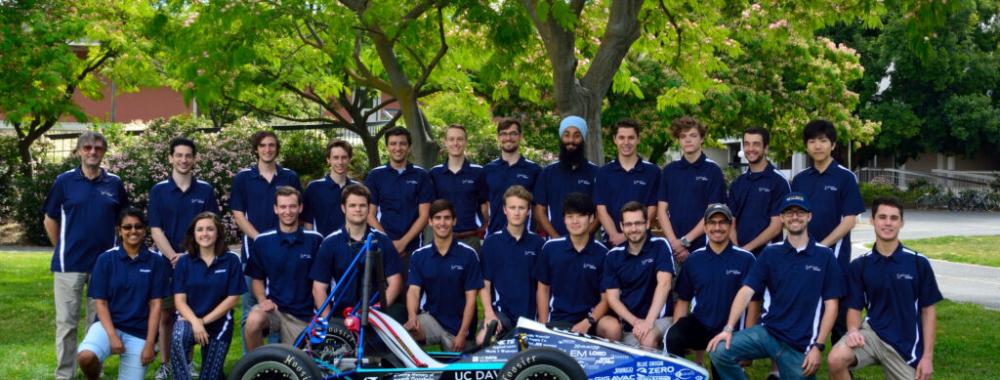
FE5
Following FE4’s design validation and successful competition performance, FE5 was designed with iterative performance improvements in mind, alongside the development of a vehicle model that would be used in the development of future cars. Weight reduction and modularity were emphasized throughout the design process.
After using the same basic setup from 2015-2017; a new powertrain was developed for FE5. The new battery featured smaller cells, reduced overall capacity, and increased packaging efficiency. In addition to better optimizing the battery for the competition environment, a central focus was placed on improving the battery’s thermal management. 3D printed side ducts directed air into the accumulator and over heat spreaders, which were placed between each cell. A prototype motor controller was built using upgraded components with higher thermal tolerances and a larger heat sink.
FE5 was tested extensively prior to competition, and data from test days was used to continually improve the vehicle model. At competition, FE5 was unable to pass the electrical technical inspection when water entered an electronics enclosure during the rain test. The team placed first in the Cost event after a complete overhaul of the Cost Report, and FE5 ultimately placed 16th overall.
Year Produced: 2017-2018
Weight: 463lb
Weight Balance: 50.6% Front | 49.6% Left
Electric Motor: ZERO Z-Force 75-7R
Output: 50 kW @ 3850 RPM
Max Torque: 140 N-m for 120 sec
Max Speed: 79.6mph
Accumulator: NCM-Cathode Li-Ion
Battery Capacity: 6.1 kWh
Suspension: Double Wishbone with Pushrod-Actuated Shock Absorber
Chassis: 4130 Steel Space Frame
Notable Features: Easily Adjustable Suspension
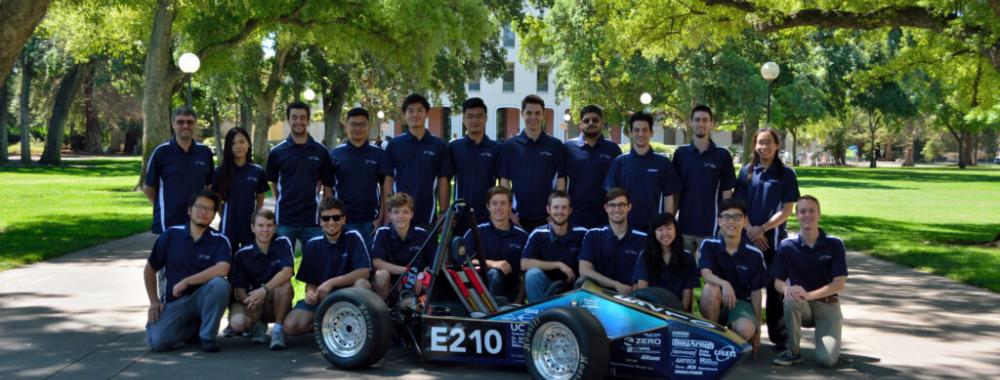
FE4
Building off FE3’s successful design, FE4 marked the beginning of our efforts to advance and optimize designs based on extensive subsystem analysis, validation, and targeted improvement of vehicle performance in specific competition settings. As with previous vehicles, modularity, backwards compatibility, and weight reduction were achieved wherever possible.
FE4 was our first vehicle to use an aircraft-grade fabric wrap in lieu of more traditional fiberglass or carbon fiber body panels, apart from a small fiberglass nosecone. The fabric panels weighed approximately ten times less per square yard than the previous year’s fiberglass panels.
The team’s enthusiasm, attention to detail, and determination led to the earliest vehicle completion timeline on record. This meant FE4 went through extensive testing before heading off to competition, another team first. As a result, FE4 was dynamically verified and tuned for optimal performance before heading off to competition.
At competition, FE4 quickly passed technical inspections and competed in every dynamic event, a major milestone for the team! Ultimately FE4 placed 6th overall.
Year Produced: 2016-2017
Weight: 486 lb
Weight Balance: 49% Front | 49.5% Left
Electric Motor: ZERO Z-Force 75-7
Output: 50 kW @ 3850 RPM
Max Torque: 140 N-m for 120 sec
Max Speed: 84 mph (135.18 kph)
Accumulator: NCM-Cathode Li-Ion
Battery Capacity: 7.6 kWh
Suspension: Double Wishbone with Pushrod-Actuated Shock Absorber
Chassis: 4130 Steel Space Frame
Notable Features: Aircraft-grade fabric body
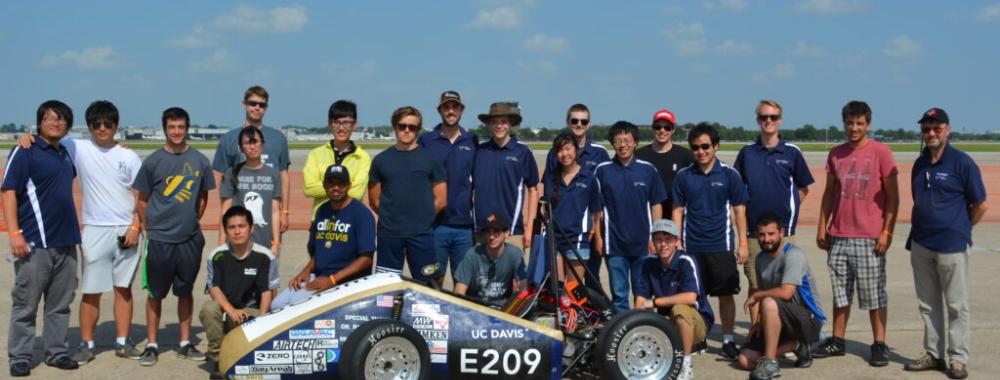
FE3
For our third electric car, we focused on starting a process of incremental improvements, rather than attempting to improve every system with a clean slate design, as was done with FE2. Our designs for FE3 were oriented around modularity and manufacturability, to leave more time for testing and validation. Weight reduction and packaging efficiency improvements were made in all systems.
FE3 placed 10th at the 2016 FSAE Electric competition in Lincoln, Nebraska.
Year Produced: 2015-2016
Weight: 519 lbs (without driver)
Weight Balance: Left/Right 49.6:50.4 | Front/Back 50.1:49.9
Electric Motor: ZERO Z-Force 75-7 Radial Flux, brushless, permanent magnet
Output: 50 kW | 40 N-m
Max Speed: 93 mph (149.67 kph)
Accumulator: Farasis pouch cell, NCM-cathode Li-Ion
Battery Capacity: 7.5 kWh
Suspension: Independent double A-Arms, push-rod actuated
Chassis: 1010 CR square and 1020 DOM round mild steel tubing
Notable Features: Modular suspension, tachometer
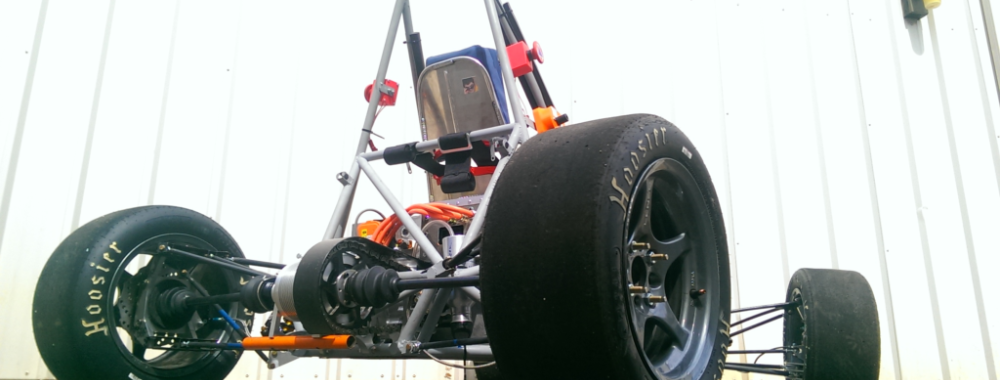
FE2
For our second electric car, we considered the design of FE1 and focused on reducing the weight and overall length of FE2, as well as system-level optimization. Rather than use two motors, it was decided that using a single motor would result in a better power-to-weight ratio by using the motor to its full potential and reducing the overall size of the battery pack. This also allowed for a significantly more compact drivetrain and a dramatic reduction in overall length when compared to FE1. An ideal reduction ratio of 6:1 was achieved by integrating a first stage planetary gearbox and second stage chain for versatility and high torque density. The suspension was designed to be tuneable using well-understood kinematics. The car also featured a custom battery management system and onboard real-time data logging. This design netted the team 9th place in the 2015 Lincoln FSAE Electric competition.
Year Produced: 014-2015
Weight: 550 lbs (without driver)
Weight Balance: Left/Right 49:51 | Front/Back 43.6: 56.4
Electric Motor: ZERO Z-Force 75-7 Radial Flux, brushless, permanent magnet
Output: 50 kW | 40 N-m
Max Speed: 70 mph (112.65 kph)
Accumulator: Farasis pouch cell, NCM-cathode Li-Ion
Battery Capacity: 7.5 kWh
Suspension: Upper A-Arm, Lower Multilink
Chassis: 1020 DOM mild steel
Notable Features: Adjustable power, interchangeable battery pack
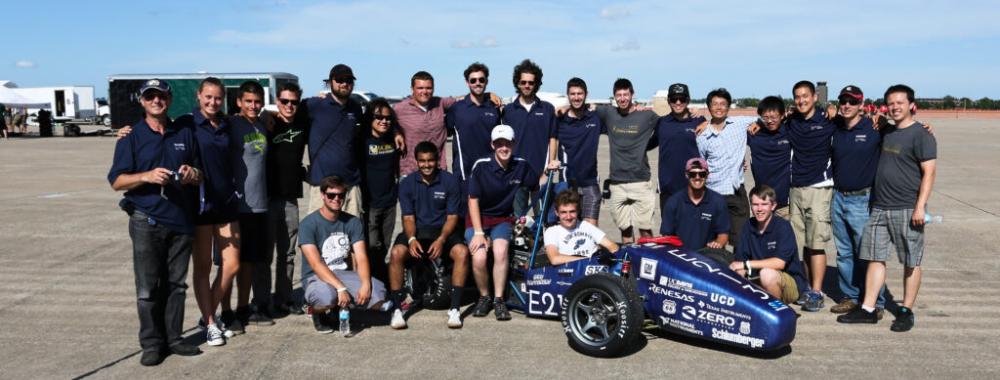
FE1
The UC Davis Formula Racing team was started in 2013 when a number of students decided to build the school’s first electric race car. Starting from the ground up, a powertrain architecture utilizing 2 ZERO motorcycle motors with an electrically controlled active differential was decided upon. The system was designed to incorporate torque-vectoring, which would allow for better handling and performance when cornering.
As a result of this design fortitude, innovation, and determination, the team placed 1st in the United States, 2nd in North America, and 3rd overall at the 2014 Lincoln FSAE Electric official competition; and was the first American team to pass the electric vehicle tech inspection.
Year Produced: 2013-2014
Weight: 654lbs (without driver)
Weight Balance: Left/Right 49.9:50.1 | Front/Back 49:51
Electric Motor: 2 Zero Z-Force 75-5 Radial Flux, brushless, permanent magnet
Output: 80 kW | 190 N-m
Max Speed: 76.4 mph (123 kph)
0-60 Time: 3.1 seconds
Battery Capacity: 6 kWh
Suspension: Double unequal A-Arm, Push-rod actuated
Chassis: 4130 Chromoly steel
Notable Features: Dual-motor torque vectoring
Before EV
As the Sierra Club’s #1 Cool School, UC Davis has built a reputation around innovation and sustainability. The school has a tremendous track record when it comes to sustainable vehicle research and development, ranging from our esteemed Future Car submissions to Professor Emeritus Andrew Frank, the “Father” of the plug-in hybrid. UC Davis’ rich automotive heritage includes a history of race car development, beginning with many years of engineering combustion-engined vehicles.
In 2009 a group of students determined to create a hybrid race car formed the UCD Formula Hybrid Team. Their first creation, FH1, was based on a Pre-Transmission, Post-Clutch integrated drivetrain; a design that optimally utilized both the electric and combustion components of the powertrain and allowed for full electric, full gas, or combined power sources. This car went on to place 3rd in the official competition at the New Hampshire Motor speedway, as well as a first place finish at the UC Irvine Invitational. The second hybrid car, FH2, was built on a redesigned chassis optimized for hybrid architecture. FH2 placed 4th at the international competition in New Hampshire and took home 1st place at Emerging Technology Day at the Indy 500.